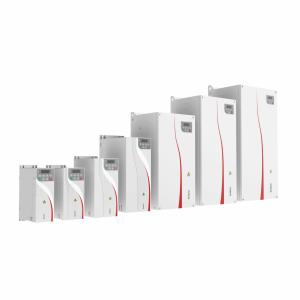
Add to Cart
HV510 High Performance Variable Frequency Drive Vector Inverter VFD Vector Frequency Converter
HV510 series frequency inverter is a new generation of high-performance vector inverter, which adopts new high-performance open and closed loop vector control technology to support asynchronous motor and permanent magnet synchronous motor control drive; excellent performance, enhanced performance and high power density design enhance industrial performance The product's ease of use, reliability, environmental stability, functional diversity, application flexibility and other advantages in the application environment have improved the design standards and optimized the installation space, etc., improving the user experience in many aspects.HV510 series frequency inverter is a new generation of high-performance vector inverter, which adopts new high-performance open and closed loop vector control technology to support asynchronous motor and permanent magnet synchronous motor control drive; excellent performance, enhanced performance and high power density design enhance industrial performance The product's ease of use, reliability, environmental stability, functional diversity, application flexibility and other advantages in the application environment have improved the design standards and optimized the installation space, etc., improving the user experience in many aspects.
HV510 series frequency inverters are widely used in driving various automated production equipment such as metallurgy, lifting, petroleum, machine tools, plastics, metal products, paper-making, textiles, printing and packaging, etc.
Technical Specification | ||
Power | Input voltage (Uin) | 380V (-15%) - 480V (+10%), three-phase |
Input power | (50Hz/60Hz)±5% | |
Input voltage | ≤3% | |
Output voltage | 0V-input voltage | |
Output frequency | 0Hz-1500Hz | |
Control | Motor Type | Asynchronous motor/permanent magnet synchronous motor |
Control mode | V/F, OLVC (open loop vector control), CLVC (closed loop vector control) | |
Speed range | 1:10 V/F; 1:100 OLVC; 1:1000 CLVC | |
Starting torque | VF: 100% (0.5Hz); OLVC: 150% (0.5Hz); CLVC: 200% (0Hz) | |
Torque precision | ≤±5%, in vector control mode | |
Torque pulsation | ≤±5%, in vector control mode | |
Speed stability | OLVC: 0.2%; CLVC: 0.1% | |
Torque response | ≤ 5ms, in vector control mode | |
Acceleration/decel | 0.0s~3200.0s; 0.0min~3200.0min | |
Torque boost | 0.0%-30.0% | |
Overload capacity | G-model: 150% 1min/5min, 180% 3s/5min | |
V/F curve | Straight-line type, multi-point type, V/F half separation mode, V/F complete separation mode | |
Input frequency resolution | Digital setting: 0.01Hz; analog setting: 0.01Hz | |
Main | Acceleration/decel eration curves | Straight-line, S-curve |
Simple PLC, multi-speed reference | 16 speed segments supported through control terminals | |
Automatic voltage regulation (AVR) | Automatically keeps the output voltage constant when grid voltage varies within a certain range | |
Fixed length control | Fixed length control | |
Built-in PID | Easily forms a closed-loop control system | |
Multi-motor switchover | With 2 sets of motor parameters, the switchover between 2 motors can be realized | |
Virtual IO | With 8 sets of virtual DI/DO, simple logic control can be realized | |
Overvoltage/overc urrent stall control | The current and voltage can be automatically limited during operation to prevent frequent trips due to overcurrent and overvoltage | |
Restart after power failure | The inverter can operate automatically when powering on again after a power failure | |
Fast current limiting | Frequent overcurrent faults can be avoided | |
Input and | Frequency reference mode | Keypad, terminal UP/DOWN, multi-reference, pulse reference, communication |
Analog input terminals | AI1, AI2: 0V-10V/0 (4)mA-20mA | |
Digital input terminals | DI1-DI5, 5 programmable digital input terminals with opto-isolation, compatible with bothsinking/sourcing inputs. | |
Digital output terminals | Open-collector output; output voltage range: 0V-24V; current load capacity: 50mA. | |
Analog output terminals | 1-channel 0V-10V/0(4)mA-20mA | |
Relay output | 1-channel Form C contact, NO+NC | |
Corresponde | Communication protocol | Modbus RTU (standard configuration); Profibus-DP, CANopen, Profinet IO, Modbus TCP/IP, EtherCAT, EtherNet/IP (optional configuration) |
Usage | Altitude | ≤1000m: no need for derating ; 1000-3000m: with current derating by 1% per 100m increased |
Ambient temperature | -25°C-+40°C (derating is allowed within 40°C-55°C) | |
Humidity | 15%-95%, no condensation | |
Vibration | 3M3, IEC60721-3-3 | |
Storage temperature | −40°C-+70°C | |
Operating place | Indoors without direct sunlight, flammable and corrosive gases, liquids and conductive particles, etc. | |
Optional accessories | Encoder card, communication expansion card, IO expansion card | |
Protections | Protection against short circuit , overcurrent, overload, overvoltage, undervoltage, phase loss, overtemperature, external faults, etc. | |
Installation method | Installed in a cabinet | |
Protection rating | IP20 | |
Cooling method | Air cooling |
Safe and reliable
Reliable structural design
Professional thermal design
Rigorous temperature rise test
Effective anti-interference design
Comprehensive protection features
Excellent performance
Advanced motor drive technology
Rich self-learning functions
Perfect braking function
Powerful overload capability
Rich functions
Diversified extended functions
Note: The optional I/O terminal expansion card and communication expansion card are in the same expansion card slot, and they cannot be installed and used at the same time
Background quick debugging software
High frequency output
Featured application software functions