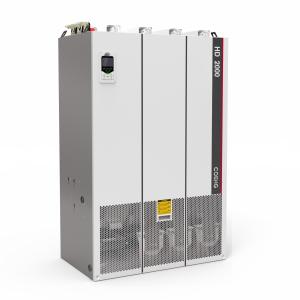
Add to Cart
The HD2000 VFD inverter, is a highly advanced single-drive/multi-drive system designed for engineering applications. It stands out due to its modular hardware and engineering software design, which allows it to effectively handle a wide range of complex drive scenarios.
With its modular hardware architecture, the HD2000 offers flexibility in configuring drive systems according to specific requirements. It can be seamlessly adapted to accommodate various motor types, power ratings, and communication interfaces. The modular approach simplifies installation, maintenance, and future expansions, making it an ideal choice for projects of different scales and complexities.
Furthermore, the HD2000's engineering software is specifically designed to provide comprehensive control and customization options. It offers a user-friendly interface that allows engineers to easily configure and optimize the drive system parameters, ensuring precise control over motor speed, torque, and other critical operating parameters. The software also supports advanced features such as adaptive control algorithms, fault diagnostics, and advanced monitoring capabilities, enhancing the overall performance and reliability of the drive system.
The HD2000 excels in handling complex drive scenarios across various industries. Whether it's controlling a single motor or coordinating multiple drives in a synchronized manner, the HD2000's robust design and intelligent control capabilities enable it to tackle demanding applications. It finds extensive use in industries such as manufacturing, material handling, mining, oil and gas, and renewable energy, where precise and efficient motor control is vital for optimizing productivity, reducing energy consumption, and ensuring reliable operation.
In summary, the HD2000 inverter stands as an engineering single-drive/multi-drive system that offers flexibility, advanced control features, and reliable performance. Its modular hardware and engineering software design empower it to handle a diverse range of complex drive scenarios, making it a versatile and dependable choice for engineers and industrial applications.
Variable Frequency Drive Specification
Basic Rectifier | Input voltage | 4:380V 〜480V,6:500V 〜690V |
Input frequency | (50Hz/60Hz)±6% | |
Output voltage | Input voltage * 1.32 (Under full-load condition) | |
Overload capacity | Relative overload at 150% of rated current for 60 seconds, maximum current (Imax), DC overload for 5 seconds | |
Operating efffciency | ≥99% Efffciency | |
Protection eunctions | Protection functions: Overheating protection, soft-start protection, Interlock protection, and more. | |
Intelligent rectifier | Input voltage | 4:380V ~ 480V,6: 500V ~ 690V |
Input frequency | 47 ~ 63Hz | |
Output voltage | Input voltage * 1.3 (Under full-load condition) | |
Overload capacity | Relative overload at 150% of rated current for 60 Seconds, Maximum current (Imax), DC overload for 5 seconds | |
Operating efffciency | ≥98.5% Efffciency | |
Protection functions | Protection functions: Overheating protection, Overcurrent protection, IGBT pass-through protection, and more | |
PWM rectifier | Input voltage | 4:380V~480V,6:500V~690V,9:1140V,A:1380V |
Input frequency | 47 ~ 63Hz | |
Output voltage | Input voltage * 1.5 (Under rated conditions) | |
Overload capacity | Relative overload at 150% of rated current for 60 seconds, Maximum current (Imax), DC overload for 5 seconds | |
Operating efffciency | ≥98% Efffciency (Including LCL fflter unit) | |
Power factor | Adjustable (Factory setting at 1) | |
Protection functions | Protection functions: Overheating protection, Overcurrent protection, Overload protection, IGBT pass-through protection, and more. |
Variable Frequency Drive Advantages
Reliable Engineering Design